Fertilizers: Fertile Investments, But…
Lazaro Gonzalez
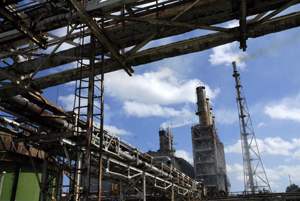
HAVANA TIMES, March 2 — “Fertilizing soils became a headache for Cuban campesinos a long time ago. After centuries of being farmed, the lack of nutrients in this land is decreasing their harvests. The rational use of fertilizers to increase crop yields is an urgent need, though it sometimes runs counter to the strategy of import substitution,” said Carlos Gonzalez, a prominent farmer in Pinar del Rio Province.
It’s very common to travel through our rural areas and hear farmers complaining about the shortage of fertilizers for their bean crops. However, every year the government spends millions of dollars to import thousands of tons of that grain.
Out of an entire industrial complex that produced more than 30 million tons of fertilizers in the 1980s, Cuba presently possesses only two factories; moreover, their combined output doesn’t reach 100,000 tons. One of them, the Rayonitro Company in Matanzas Province, produces only physical mixtures; while the more important factory, the October Revolution plant in the town of Nuevitas in Camaguey Province, also makes ammonium nitrate in its two variants: technical and fertilizing.
Renovating flows
Time is unforgiving, and so is the absence of investment. Many of the facilities at the Nuevitas factory evidence cumulative deterioration, some of which is now irreparable. In others, the equipment works thanks only to the genius, sacrifice and sense of ownership of the workers, especially those responsible for maintenance. Until two years ago, all the equipment used in the factory dated back to its establishment – in 1975.
With the goal to restore the original capacity of the ammonium nitrate plant (200,000 tons a year) starting in 2008 the plant began a technological modernization and repair process in collaboration with member-countries of the Bolivarian Alliance for the People of Our America (ALBA).
“For this it was also necessary to restore the auxiliary services — like water treatment, and the cooling and instrumentation of air — as well as get the nitric acid plant up and running since it supplies the essential raw material for ammonium nitrate,” explained Abilio Jimenez, the head of the Integrated Management Initiative.
According to its own workers, this latter plant — the only one in Cuba — experiences bottlenecks in the final production. Iraida Fabre, a veteran shift supervisor with 26 years of experience in the field, said the flow of water to supply the boilers was a headache until recently. “We had some 6,000 volt pumps that, due to their age, couldn’t meet the need.”
With the recent installation of a new German pump, which delivers high pressure output to supply 40 cubic yards of water per hour, the situation has turned around. “Previously we manufactured some 92 tons of nitric acid in each shift, now we produce up to 98. We can now satisfy demand for the maximum production of ammonium nitrate,” Fabre said.
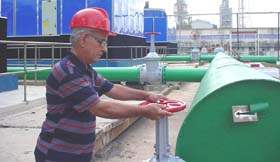
To improve plant efficiency, 10 platinum meshes were acquired overseas (though these are still insufficient) and the plant’s turbo-compressors are undergoing capital repairs to raise the pressure of the gas mixture.
Infertile paradoxes
Another of the serious problems suffered by this factory was the technical state of the water cooling towers. This was corrected this past July when 12 modern Spanish towers began functioning with an automated system directly tied to production demand.
Ammonia compressors, evaporating condensers, catalysts and network elements are some of the fruits of this investment process that simplifies the industrial installation and increases efficiency in the use of ammonia, electricity and water.
To date, investment for these upgrades has been considerable, said Jimenez. “Our aim is to recover that amount in a little more than two years.” The additional capacity has reached 90,000 tons a year and this should be increased up to 140,000 very soon, according to the manager.
“Based on our feasibility study, once we recover our original capacity we anticipate producing 50,000 tons for export and 150,000 for the domestic market,” he noted. However, at the moment the firm’s managers are more certain about the potential for export than that for domestic consumption.
Today we work according to orders from the ministries of Agriculture and Sugar, which are very low. We produce less than what we can. This year we’ve produced barely 30,500 tons, a third of the available capacity,” Jimenez explained.
The plant is often off line; in 2010 we only worked 115 days. Eacg time we get the plant going we spend a lot of energy because start up takes 18 to 20 hours. And after ammonia, electricity is our principal raw material. When production stops we reassign the majority of the employees to work on making the capital improvements, but some of them have to be temporarily laid off.”
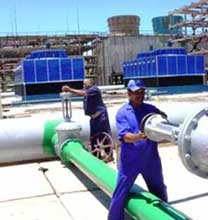
The nitrate of technical ammonium produced at the October Revolution plant is used to manufacture anesthetic and explosive gases, which are demanded most on the international market. The principal markets are Venezuela, the Dominican Republic, Colombia and Suriname. This year the company has exported more than 4,500 tons. A ton of ammonium nitrate sells for about $300 dollars.
Full speed ahead
Among the secondary production lines at this company are shaving lotion, cologne, whitewash, electrolytic solutions (battery acid), and cleaning products such as “nitrofuman,” which is useful in cleaning bathrooms.
“This year, like last, we’ve made those products working on a shoe string, looking for materials at the Raw Materials Recovery Company, having fundraisers, etc. because the situation with bottling containers hit us hard. Right now we’re battling to be in the black, because exports don’t leave us with domestic currency,” Jimenez complained.
Recently the plant launched calcium nitrate on the market for the first time. This fertilizer, based on lime and nitric acid, can substitute for certain imports. The problem is that while the imported product arrives solid at a hundred percent concentration, here it’s produced in a form that is 50 percent liquid because the plant doesn’t possess the technology for drying it. “However tests carried out in local greenhouses have turned out very positive,” Jimenez asserted.